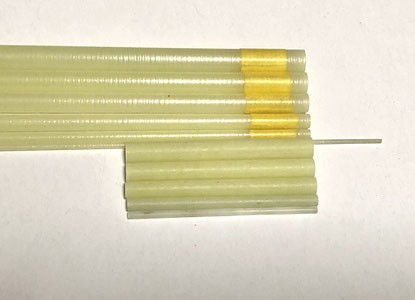
グラスロッドは以前はブランクスを入手して、組み立てのみをやっていましたが、自分ブランドのブランクスを作製するにあたっては、2ピース状態で入手して、自分で6ピースに切断してフェルールを作製しています。
理由は2つあって、
1つは、自分でカットできるので、2ピース、4ピース、6ピース、場合によっては8ピースにも加工可能です。
長さも6'09"~7'03"までバリエーションを持たせることができるのです。
2つ目は、自分でブランクカットできるので、カット部分を旋盤で綺麗に形状を整えることができるのです。
グラスロッドメーカーであっても、このカット部分が綺麗ではないメーカーが結構あります。
自分でカットするメリットは上記のようなものですが、反対に自分でカットすると、フェルール部(私の場合はスピゴットフェルールです)を自分でカットして接着して、すり合わせする工程が必要になります。
6ピースの場合、5つのスピゴットフェルールのカット、接着、すり合わせが必要であり、1日仕事になります。
フェルールのすり合わせが終われば、グリップの接着です。
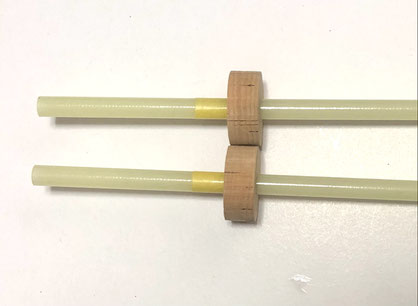
コルクの穴あけに関しては前々回のブログで書いているように両方向からのドリル加工で穴径を広げています。
コルクは11個接着する場合が多いです。
一番グリップエンド側のコルクに関しては、エポキシ系接着剤で位置決めして接着します。
これは、リールシートを仮固定して、グリップ位置を確認した後にマーキングして、その位置に接着します。
なぜ、1個目はエポキシで接着するのか?
これは単純に強固に接着して、他のコルクを接着後に加圧固定するときに位置ずれしないようにとの配慮です。
他のコルクに関しては木工用ボンドで接着しています。
コルクの穴径はブランク径よりも1mm程度小さめに加工して、圧入接着するようにしています。接着剤塗布後も加圧して接着するので、接着後はコルクのボイド部分には接着剤が充填されているので、浸水によるトラブル等は皆無です。
反対に、成形されているコルクグリップをブランクに接着する場合は、個別で接着するようにブランクに対して圧入することが不可能なのでどちらのやり方が品質の高いやり方かはわかると思います。
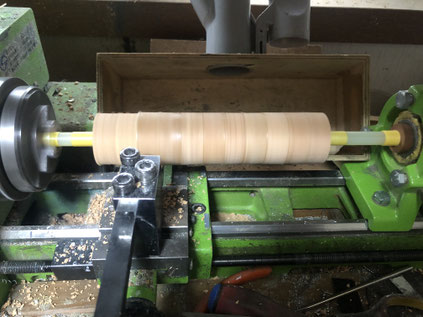
コルク接着後はコルク成形です。
旋盤にチャックして成形するのですが、その時に役に立つのが、振れ止めです。
私はこの振れ止めに内径15mm程度のベアリングを固定しています。
仮に振れ止めに固定したい部分のブランク径が10mmとした場合、ウッド材で外径15mm、内径10mmのスペーサーを加工して、振れ止めのベアリングにこのスペーサーを固定し、これにブランクを通して振れ止めしています。
この状態でコルクの成形は、最初はバイトで加工します。
案外バイトに負荷がかかるので、幅の狭い突っ切りバイトなどで成形していきます目標径+1~1.5mm程度までバイト加工して、その後サンドペーパーで成形します。
傷つけたくないブランクにはマスキングテープを巻き付けています。
このコルク成形時などは6ピースの短いブランクはやり易いです。
#120,#240,#400,#800の順で仕上げます。#400で成形後、コルクパテで凹み部分を修正し、硬化前に再度#400で研磨して、#800で仕上げると綺麗に仕上げられます。